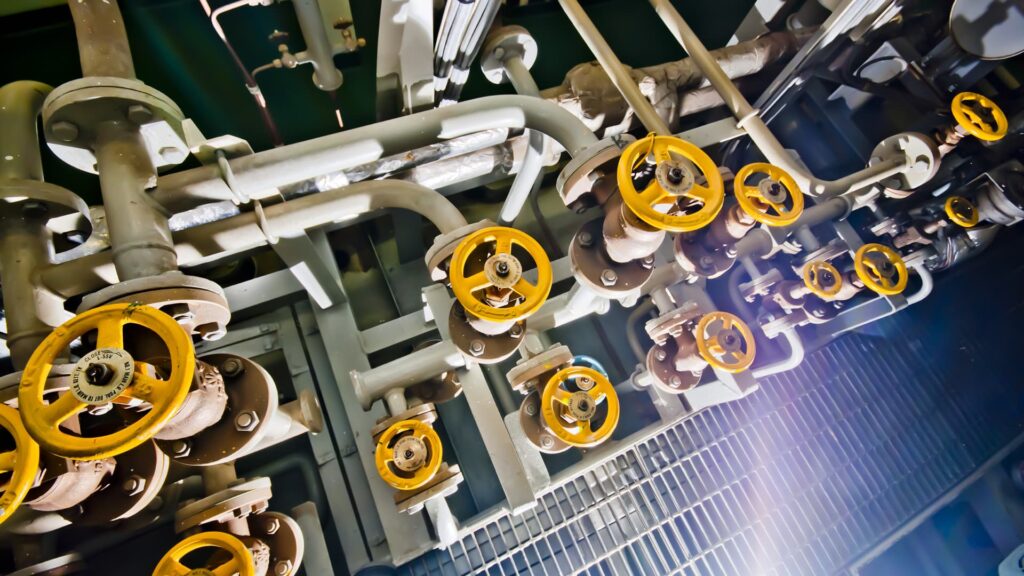
Valves on Ships: Essential Components for Smooth Operations
Valves on ship play a critical role in the operation and safety of ships, ensuring that fluids like water, fuel, and hydraulic oils flow seamlessly through the vessel’s complex systems. These components are the backbone of maritime engineering, facilitating various processes from propulsion to firefighting. This article delves into the significance of valves on ships, their types, maintenance practices, and tips for optimal usage.
Valves on Ship the Importance of Valves in Ship Operations
Valves are indispensable components in maritime systems due to their multifaceted roles:
- Flow Regulation: Valves control the flow of fluids, ensuring smooth operations of critical systems such as cooling, lubrication, and fuel supply.
- System Safety: By isolating sections during maintenance or emergencies, valves prevent accidents and ensure operational safety.
- Efficiency Optimization: Properly functioning valves contribute to energy efficiency by maintaining optimal fluid pressure and flow rates.
- Versatility: From ballast systems to cargo operations, valves are vital for various shipboard tasks.
Their reliability is non-negotiable, making their design and maintenance a top priority for ship operators.
Types of Valves Used on Ships
Ships utilize a wide range of valves tailored for specific purposes. Here are some common types:
- Gate Valves: Ideal for on/off control in pipelines, gate valves are robust and suitable for high-pressure applications.
- Globe Valves: These are used for precise flow regulation, particularly in fuel and cooling systems.
- Ball Valves: Known for their reliability, ball valves provide quick shut-off capabilities.
- Butterfly Valves: Lightweight and compact, butterfly valves are used in low-pressure systems such as air and water lines.
- Check Valves: Preventing backflow, check valves are critical in systems like bilge and ballast operations.
- Pressure Relief Valves: Ensuring system safety, these valves release excess pressure in hydraulic and steam systems.
Each valve type serves a unique function, making their selection crucial during ship design and operation.
Valves on Ship Common Applications of Valves on Ships
Valves are integrated into various systems across a ship. Key applications include:
- Ballast Water Management: Valves control the inflow and outflow of ballast water, ensuring stability and compliance with environmental regulations.
- Fuel Systems: Regulating fuel supply to engines and generators for consistent performance.
- Firefighting Systems: Ensuring rapid response in emergencies by controlling water and foam supply.
- Cooling Systems: Maintaining optimal temperatures in engines and auxiliary systems.
- Cargo Handling: Facilitating the loading and unloading of liquid cargo like oil and chemicals.
Their strategic placement and functionality are essential for operational efficiency and safety.
Valves on Ship Maintenance and Inspection of Ship Valves
Regular maintenance of ship valves is essential to avoid malfunctions and ensure longevity. Best practices include:
- Routine Inspections: Check for leaks, corrosion, and mechanical wear during routine ship maintenance schedules.
- Cleaning: Remove debris and sediments that may hinder valve operation.
- Lubrication: Apply appropriate lubricants to moving parts to reduce friction and wear.
- Pressure Testing: Verify that valves can withstand operating pressures without leaks.
- Replacement: Replace worn-out or damaged valves promptly to prevent system failures.
Adhering to these practices reduces downtime and enhances overall ship performance.
Challenges in Managing Valves on Ships
Despite their importance, managing valves on ships comes with its own set of challenges:
- Corrosion: Constant exposure to seawater and harsh conditions accelerates valve corrosion.
- Wear and Tear: Continuous operation and high-pressure environments lead to mechanical wear.
- Accessibility: Valves located in confined or hard-to-reach spaces can complicate maintenance efforts.
- Compliance: Adhering to international regulations, such as MARPOL and SOLAS, requires regular audits and documentation.
Overcoming these challenges demands proactive maintenance and the use of high-quality materials during valve selection.
Tips for Choosing the Right Valves for Ships
Selecting the appropriate valve type and material is critical for ship efficiency and safety. Consider the following tips:
- Understand System Requirements: Analyze the pressure, temperature, and flow characteristics of the system.
- Material Selection: Choose corrosion-resistant materials such as stainless steel or bronze for marine environments.
- Size Matters: Ensure the valve size matches the pipeline specifications to avoid inefficiencies.
- Automation: Consider automated valves with remote control capabilities for enhanced operational convenience.
- Certifications: Opt for valves that meet international maritime standards and certifications.
Making informed decisions during valve selection minimizes risks and optimizes shipboard operations.
Valves are the unsung heroes of maritime engineering, ensuring the smooth and safe operation of ships. By understanding their types, applications, and maintenance requirements, ship operators can enhance their vessel’s efficiency and safety. Whether you’re managing a cargo ship or a luxury yacht, investing in high-quality valves and proactive maintenance is key to navigating the seas with confidence.